The Art of Bronze Sculpture:
Lost Wax Casting Method Explained
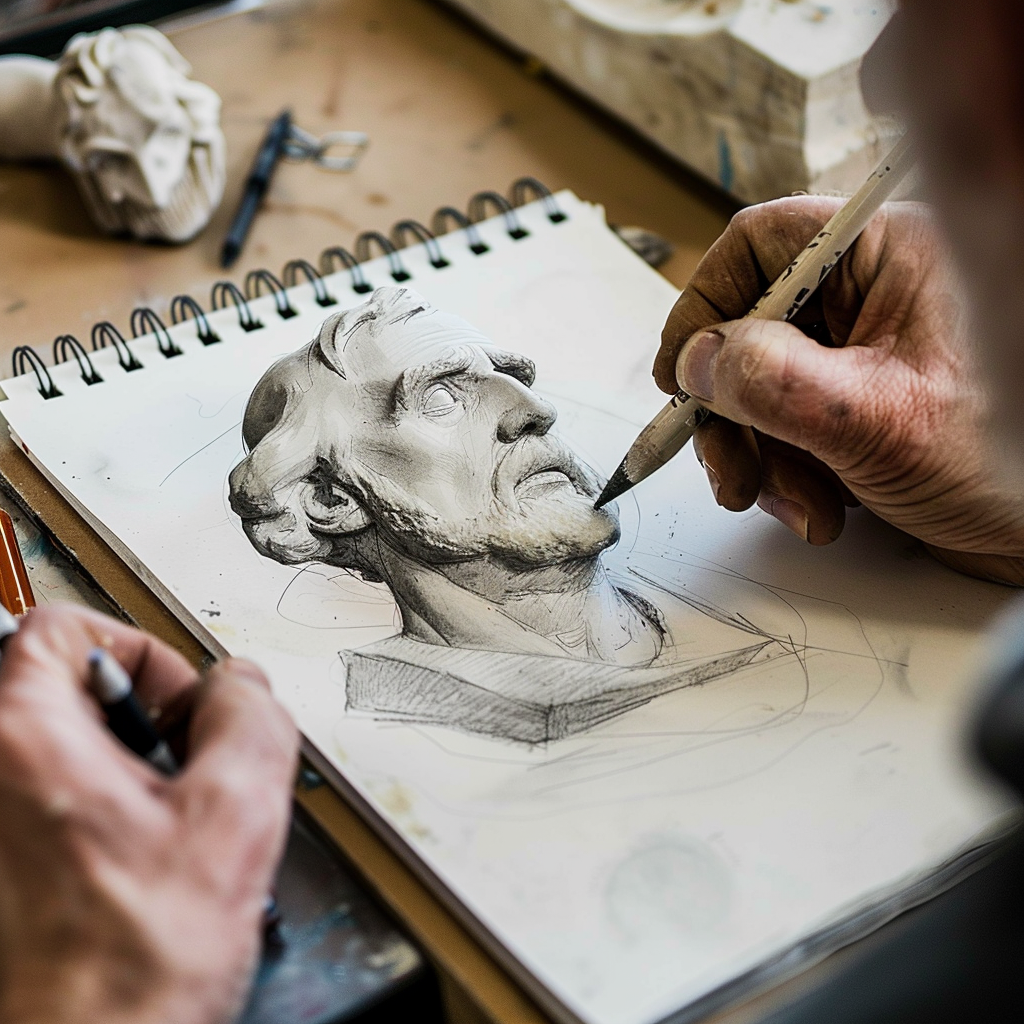
Conceptualization, Sculpture Design
Every bronze sculpture begins with a vision. Artists sketch their ideas, considering form, posture, and expression, to ensure the final piece conveys the intended message. These initial sketches are crucial for the subsequent modeling phase.
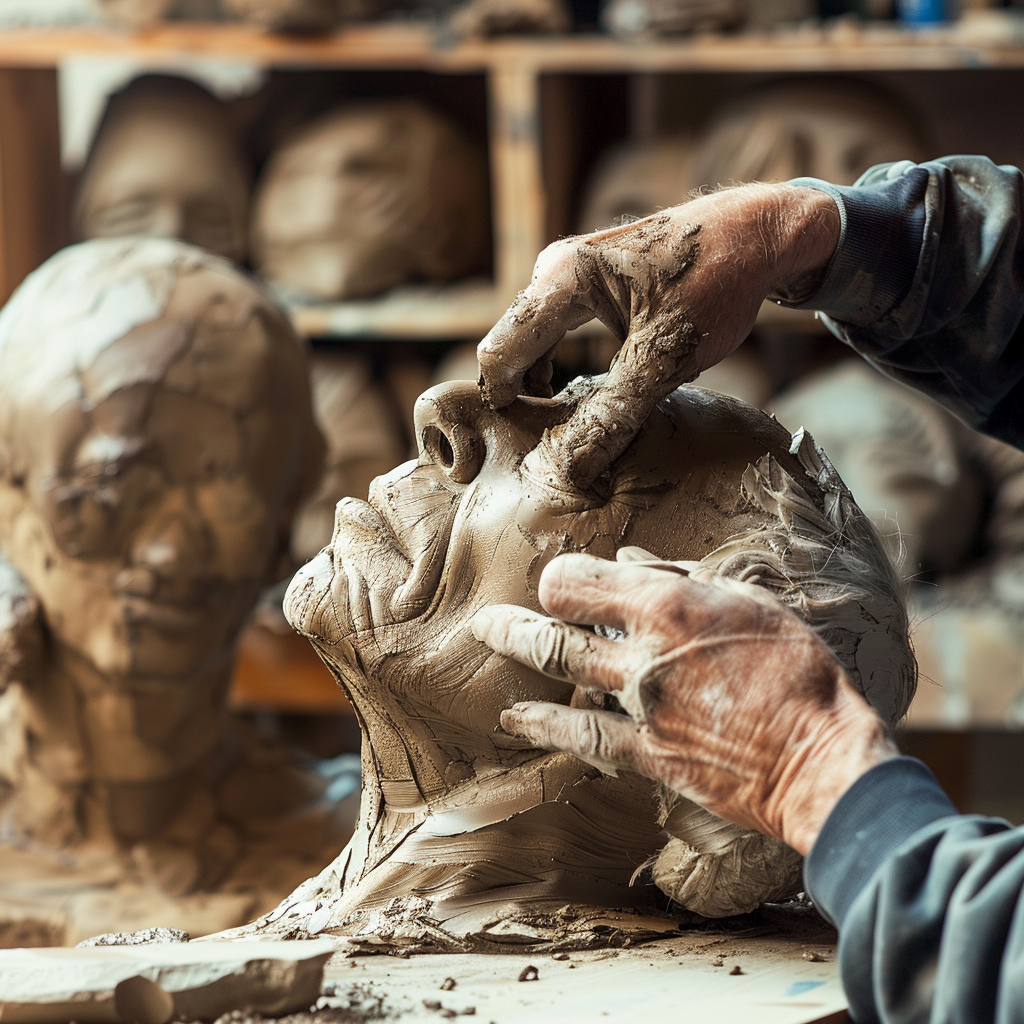
Sculpture Modeling, Clay Model
Using the sketches as a guide, sculptors craft a model, typically from clay or wax, meticulously shaping it to capture every detail. This model serves as the blueprint for the bronze sculpture, embodying the piece's essence.
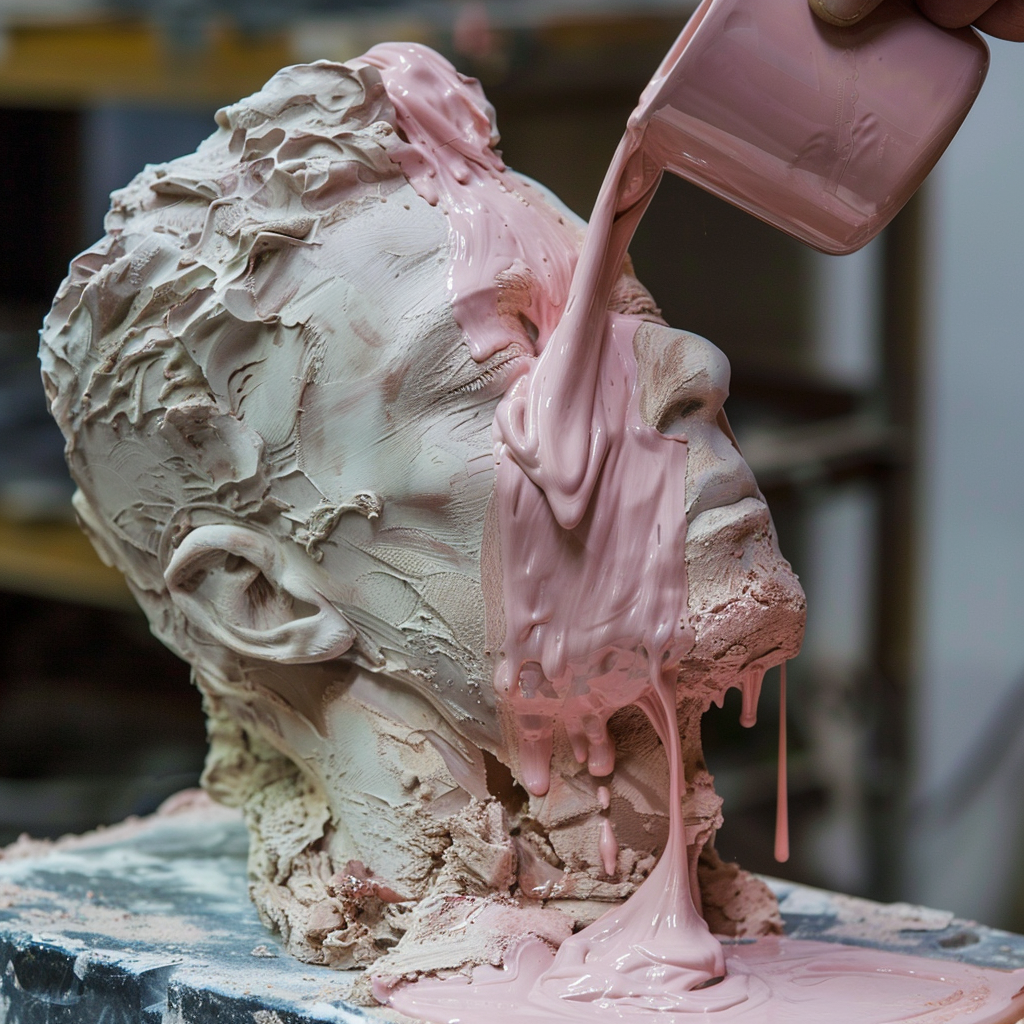
Mold Making, Sculpture Replication
Once the model is complete, a mold is created around it. This mold must capture every nuance of the model, as it's crucial for the casting process. The mold is usually made from materials like plaster or silicone, which can accurately reproduce the model's surface.

Wax Casting, Detail Reproduction
A wax copy of the sculpture is produced from the mold. This step is critical, as the wax copy needs to replicate the original model's details precisely. It's this wax form that will eventually be cast in bronze.
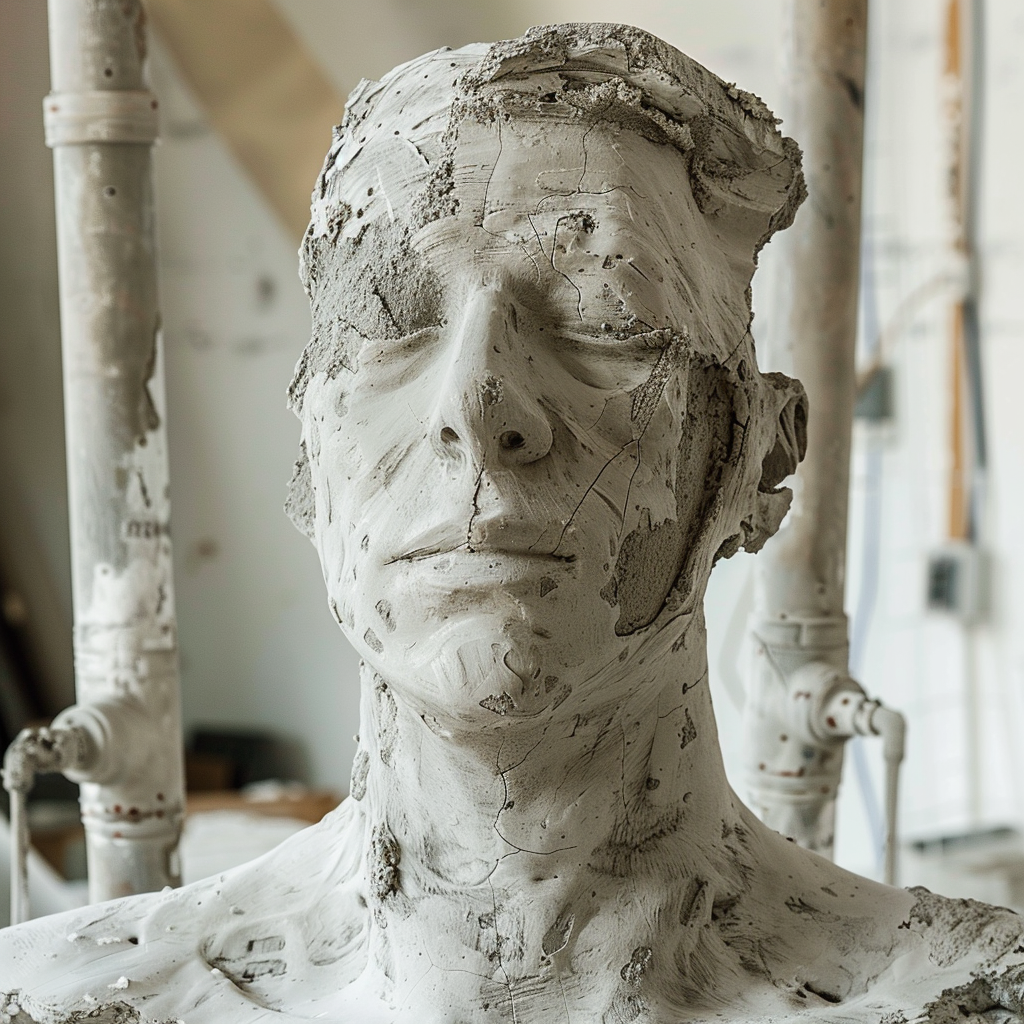
Spruing, Investment Casting
The wax model is then attached to a sprue system, ensuring even bronze flow during casting. The model is then encased in a ceramic shell, known as investing, which will hold the molten bronze.
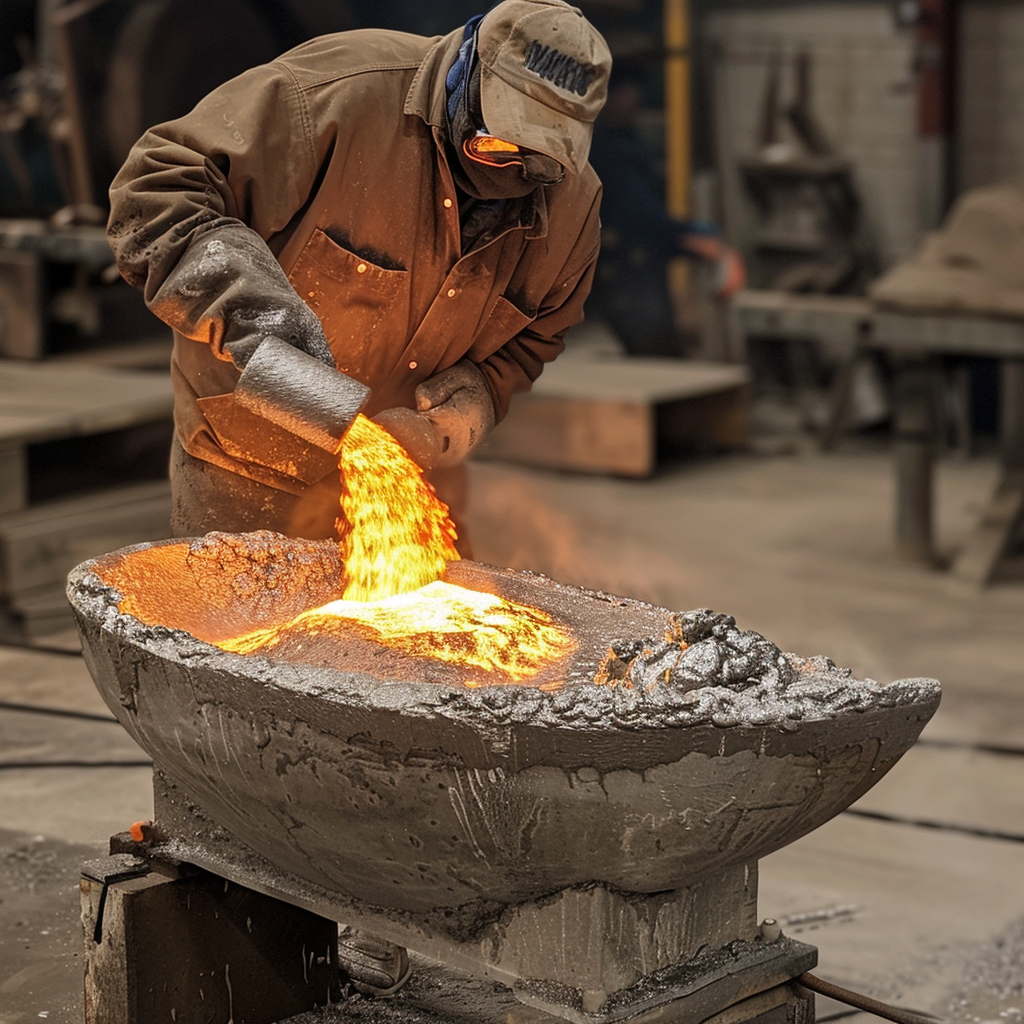
Bronze Pouring, Metal Casting
The investment is heated, melting away the wax and leaving a cavity in the shape of the sculpture. Molten bronze is poured into this cavity. Once the bronze cools and solidifies, the investment is removed, revealing the bronze sculpture.
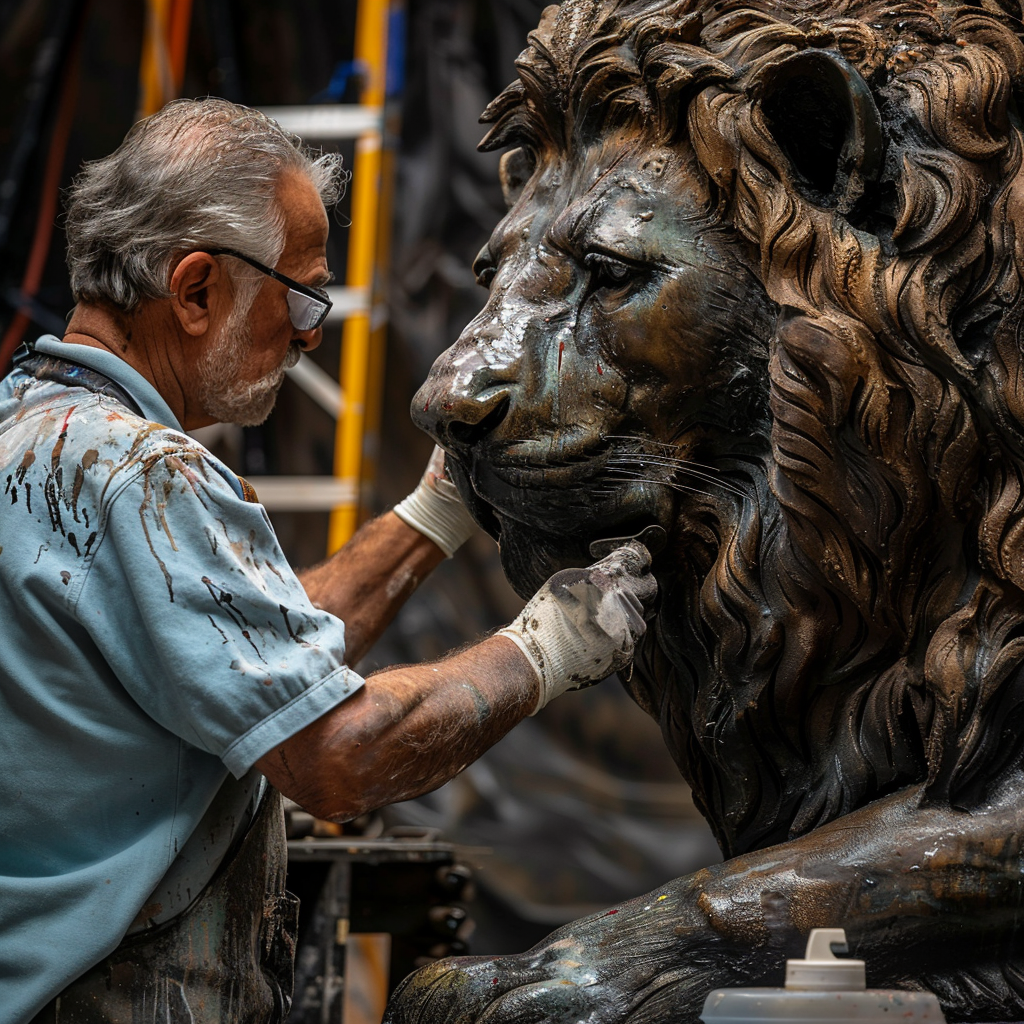
Sculpture Finishing, Patina Application
The final steps involve refining the sculpture's surface, repairing any imperfections, and applying a patina to achieve the desired color and texture. This meticulous finishing process ensures that each bronze sculpture is a masterpiece of art.
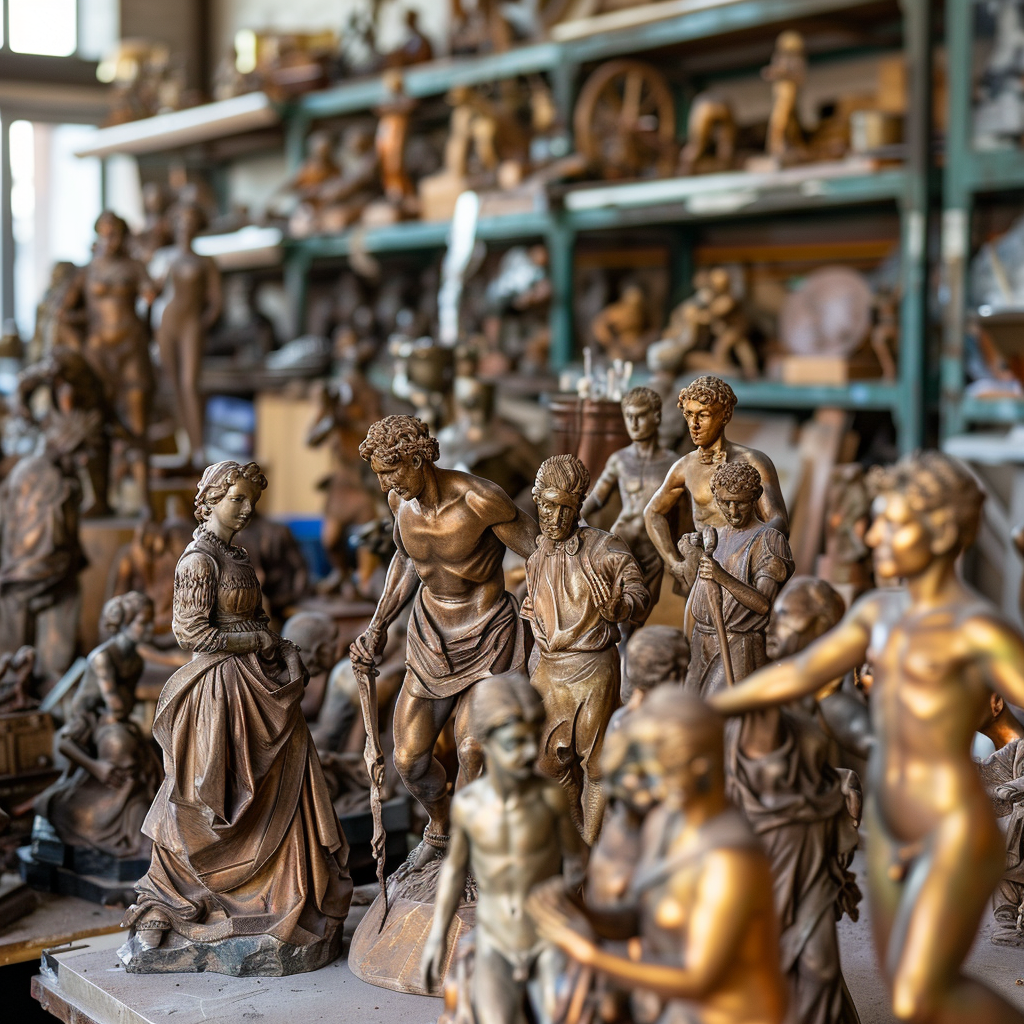
The lost wax casting method is a testament to the blend of creativity and technical skill involved in creating bronze sculptures. Through this detailed process, ideas are transformed into tangible art, each piece imbued with its own unique story and beauty.
Subscribe to our newsletter
Promotions, new products and sales. Directly to your inbox.